Competence on laser process
Cutting and welding sheet metal through the laser process requires gases and mixtures of high purity and production precision. In Nippon Gases, through decades of experience in the production of gas and in collaboration with the best manufacturers of laser systems, we have developed production techniques capable of meeting the strictest requirements of manufacturers and beyond.
CO2 have a responsibility to create light emission for effect of energy excitation, that after polarisation, became laser beam.
The job of this gas is double, into the source accumulate electron to move to CO2 when it needs to maintain excitation itself, in second as protection of metal sheet during the cutting process.
Used into the laser source, the effect is to maintain system cooled.
Normally oxygen is a problem on laser cutting process, but, as in oxyfuel cutting technology, to cut carbon steel, the function of oxygen is to burn the carbon present into the middle steel to help the fusion.
To supply gas to a laser cutting system it is essential to know fluid dynamics. In fact, it is essential to guarantee high flow rates at high pressures without affecting the machine with pressure changes.
It is equally important to maintain the purity of the gases contained in the containers up to the point of use. In this case too, the experience and passion that distinguishes us have allowed us to design specific equipment for gas management.
Metal reactivity
Every single material requires a
specific root protection gas.
Carbon steel, stainless steel, aluminum, titanium and
many others have metallurgical different characteristics
and a reactivity towards air.
During the laser cutting or welding phases it is essential
to protect or bring heat to allow the process, while the
absence of pollutants allows to exploit all the power of
the laser sources, whether CO2 or fiber.
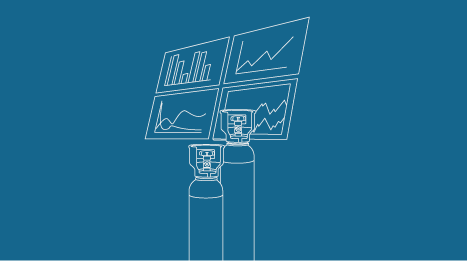
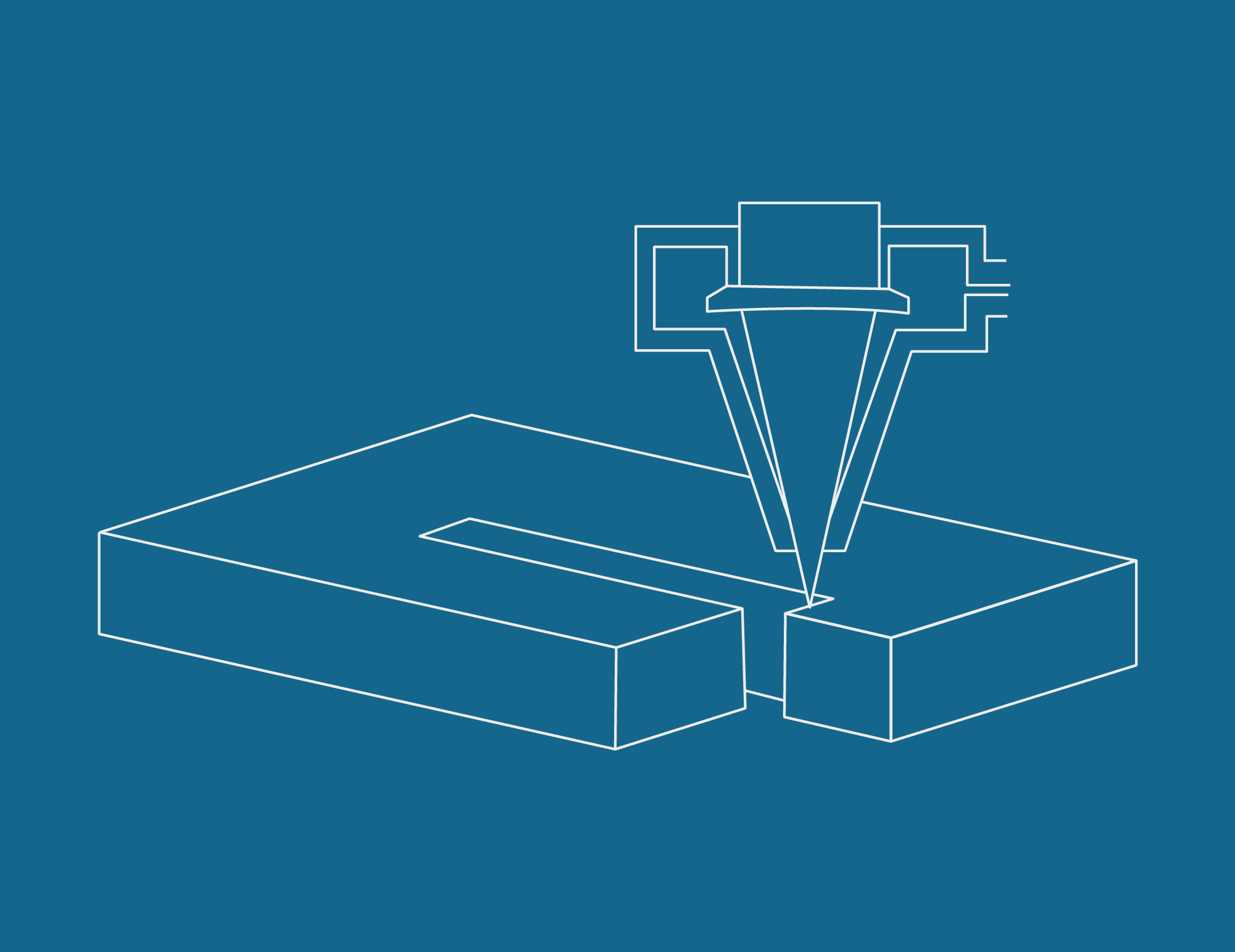