Competent and professional Customer Service
In the last few years, the 3D printing process has evolved, thanks to the development of fibre resources and a greater focus precision of the laser beam. Nevertheless, this complex process in repeatability still needs more studies and improvement to tame the lack of standards.
The influence of gases in the metal additive manufacturing process.
3D printing processes can be of different types: PBF, EBM, DED, FDM, and the most recent one WAAM. There are also many different metals, often noble ones, that can also be processed, reason why this is an expensive process.
All these different processes have a common characteristic, which is to protect the manufactured product from oxidisation during construction and heat treatment phases. So, to preserve the metallurgical characteristics of the metal powder essential to obtain the finished product, it is important to use high-quality gas.
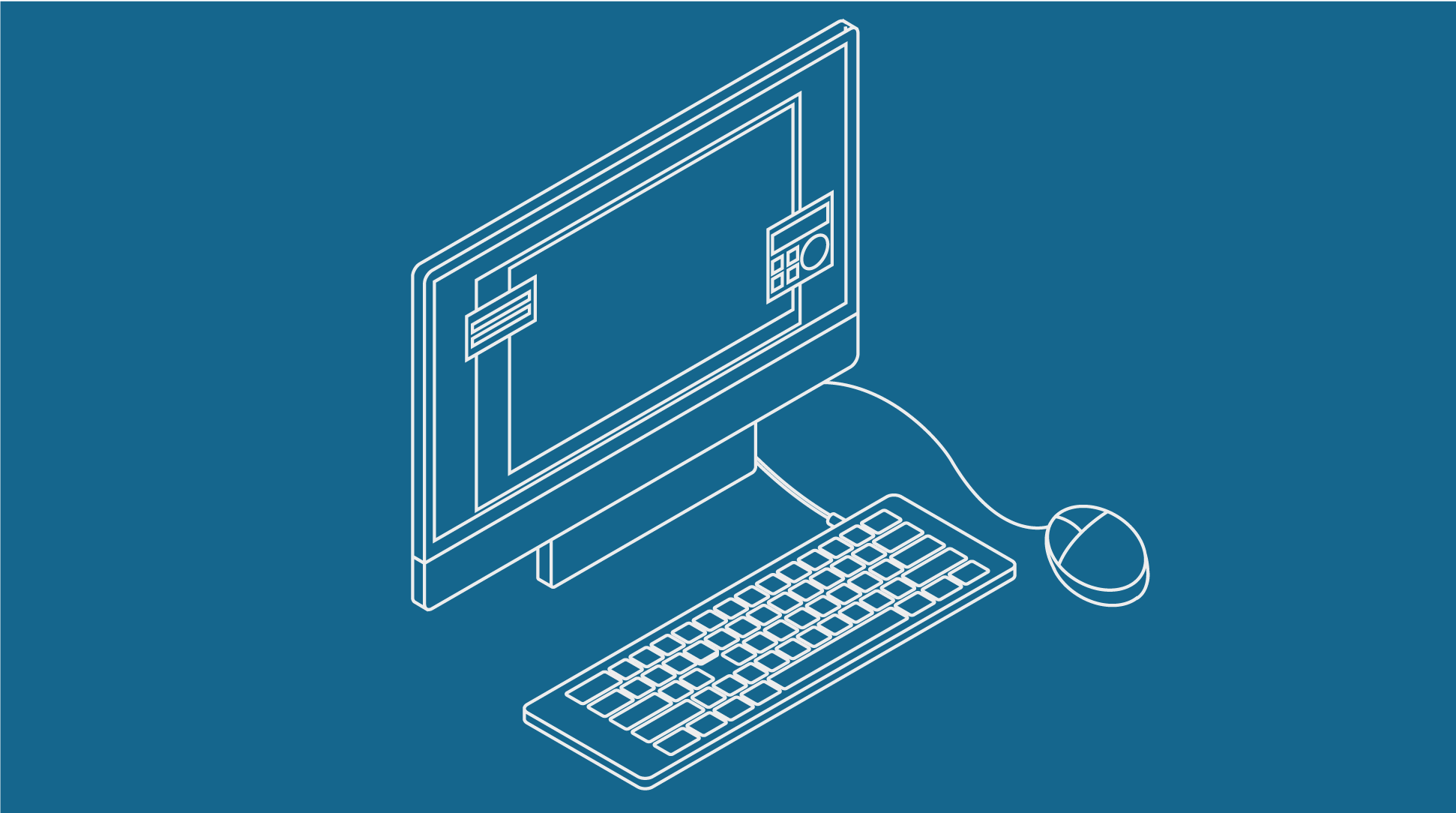
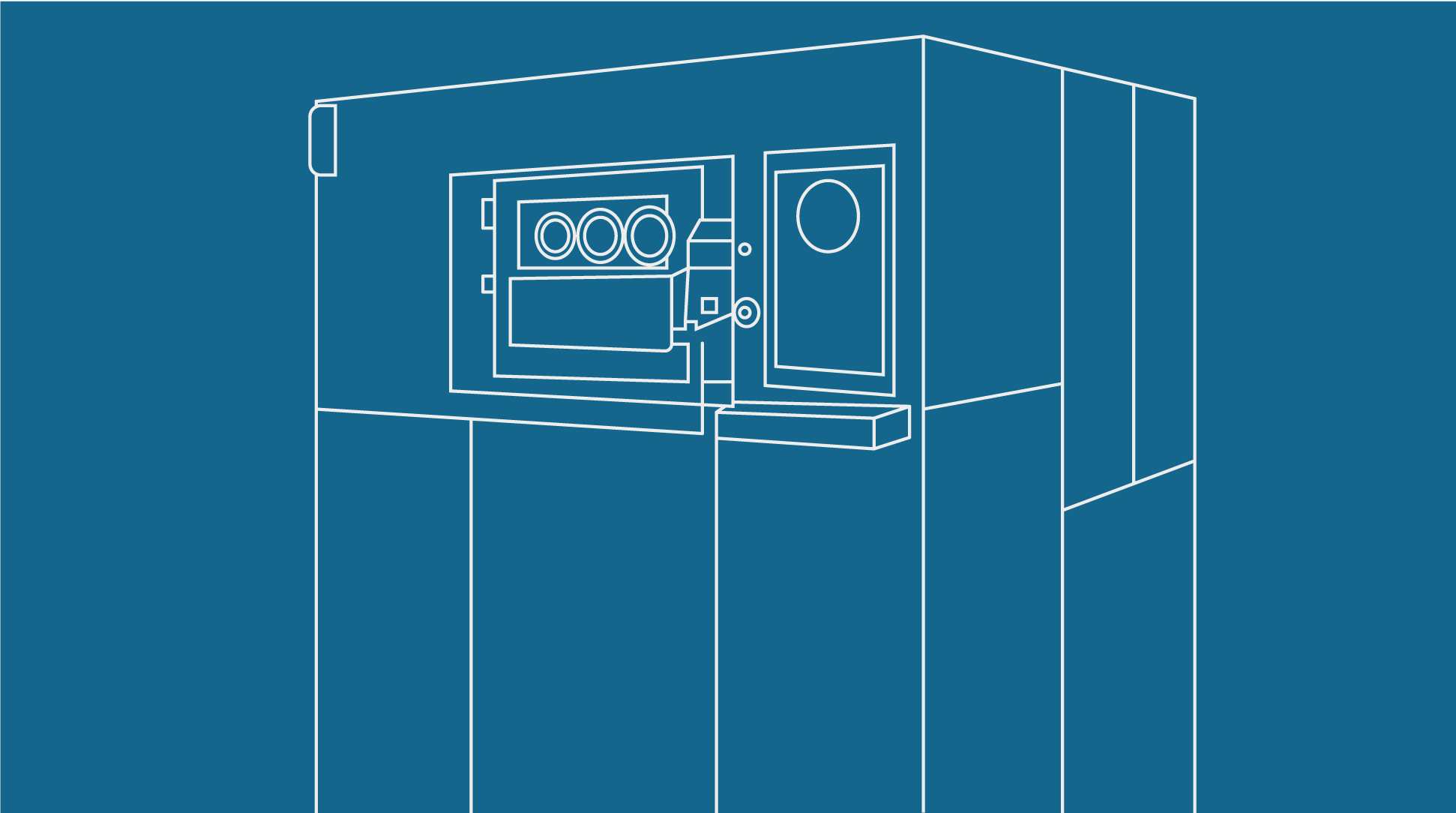
3DPro® MiruGas® acquires all gas management data, also through loT technology.
The information collected is recorded during the entire process, delivering a continuous and closely monitored process, which will allow us to check all changes and anomalies that may occur in real-time. So, thanks to 3DPro® MiruGas®, it is possible to intervene promptly, erasing loss from the equation.